August 2024
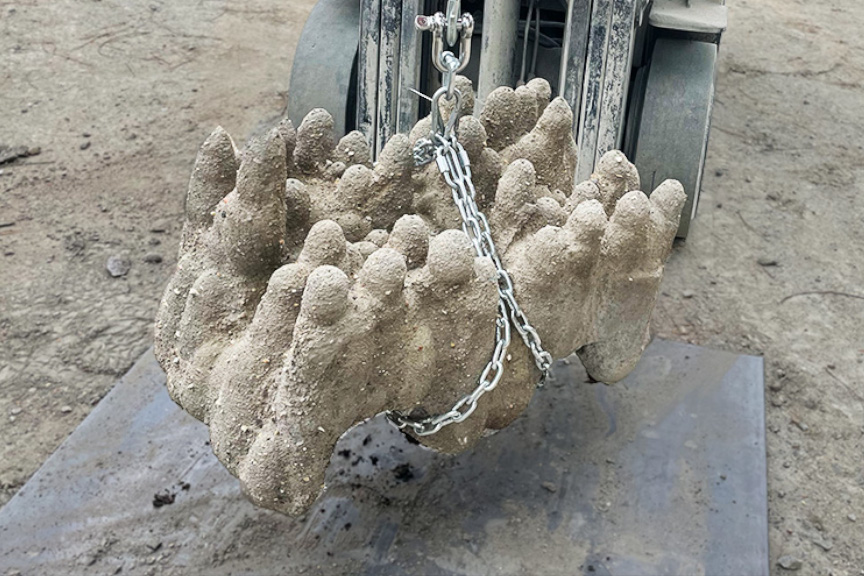
A precursor “Wave Brush” ExoForm reef made of dredged sediments from the Port of Baltimore, completed before the York River project. The ExoForm is pictured during a drop test onto a steel plate to gauge its strength. (Leonard Nelson/Natrx)
by Jim Morrison, Virginia Mercury
In 2022, RISE, the Norfolk-based nonprofit that creates challenges seeking innovative solutions to the climate crisis, issued a call for new approaches to dealing with mud, the spoils of dredging.
Virginia’s Middle Peninsula Planning District Commission and the Eastern Shore had $20 million in ready projects, the challenge noted, which would yield an enormous amount of spoils (one study concluded there will be 100,000 cubic yards of dredging material annually in coastal Virginia). While there is an overwhelming demand for clean sand from dredging to replenish beaches, the dirtier spoils dominated by clay have been considered worthless and expensive to dispose of.
RISE asked competitors to re-imagine how that material could be recycled in economically sustainable ways.
Leonard Nelson, co-founder of Natrx, a technology company focused on coastal resiliency, thought he had the answer: examine how the mud could be used as a concrete substitute for printing barriers to protect the shoreline or create oyster reefs. But when the Raleigh-based company began using the $200,000 grant funded through RISE by Go Virginia to analyze the mud in the Middle Peninsula, they found it was rich in clay, too rich to be used in that way.
For an answer, the company turned to the wisdom of the ancients – the recipe for Roman concrete.
Converting clay to concrete
In recent decades, researchers have probed samples from Roman concrete structures like tombs, aqueducts, and breakwaters to uncover why they endure when modern concrete may crumble after only a few decades. They haven’t been successful, but they have developed an understanding of its composition, which includes clay.
Natrx tested and validated converting the clays from dredging in the York River into a substitute for some of the cement in concrete, lowering its carbon footprint by nearly half and the cost by nearly two-thirds. Not only is it cheaper, but it is also stronger than traditional concrete.
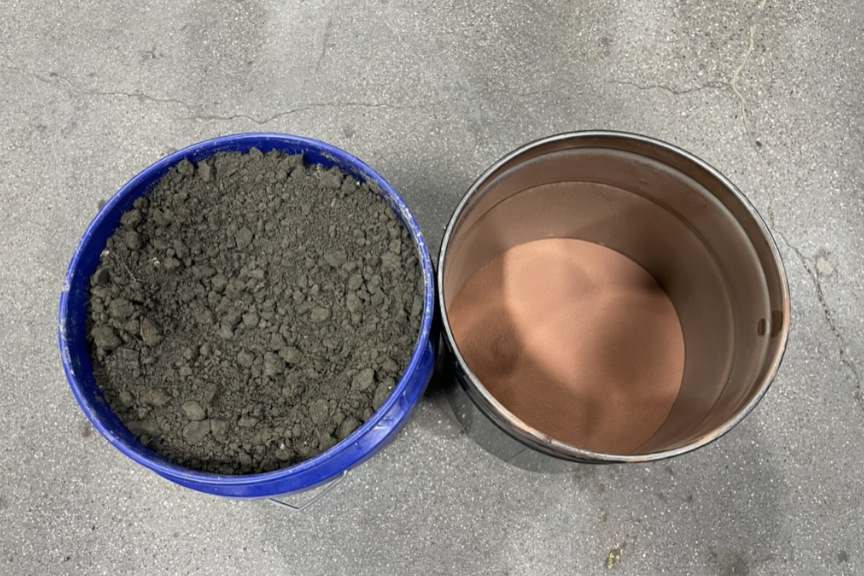
The buckets display dried, black mud from the York River (left) and reddish-brown calcined clay product, which will be converted into a substitute for some of the cement in concrete. (Leonard Nelson/Natrx)
Nelson and Natrx co-founder, Matthew Campbell, collaborated with an East Carolina University researcher to publish a paper earlier this year with the proof. Two other studies previewed their findings.
“This process has been around for a long time and unfortunately hasn’t been industrially adopted,” said Nelson, who has a chemical engineering degree.
The solution, Nelson noted, is an opportunity for cash-strapped rural areas which may have to pay a tipping fee to landfills to deposit the spoils, which could cost millions of dollars.
Natrx plans to supplement the concrete with dredging spoils in its patented custom ExoForms, structures that protect shorelines from erosion and create a habitat for oysters and fish.
The Raleigh-based company won a 2020 coastal resilience competition through RISE for a $280,000 loan to purchase a 3-D printer to create the forms, which can be fabricated in a variety of shapes and sizes. They have been deployed in two dozen projects from the Chesapeake Bay to the Gulf of Mexico.
In contrast to walls or riprap, they can be installed in days instead of months. They use about one-tenth the tonnage of traditional riprap transported from inland at less than 45% of the cost, according to an economic analysis commissioned by the company. Creating the concrete supplement locally would decrease the need to import cement; the United States is by far the world’s largest cement importer.
“There’s an obvious circular economy play there to replace some of that imported, high transportation-intensive cement that’s high carbon with a low-carbon clay that is derived from these dredge sediments,” Nelson said.
The recipe for modern concrete created two centuries ago in Great Britain is a mix of several materials: water; fine aggregates or sand; coarse aggregates or gravel; chemical additives; and Portland cement, which binds the ingredients. Creating that cement requires using fossil fuels to heat a clay and limestone mixture to more than 2,500 degrees, releasing about 1,300 pounds of carbon dioxide for every 2,200 pounds produced.
Modern concrete production is second only to water as the world’s most consumed material and studies show it accounts for about 7 % of greenhouse gas emissions.
Supplementing concrete with dredge spoils fights climate effects in multiple ways. The Natrx concrete process reduces emissions, which slows global warming. Deploying the material in ExoForms helps protect shorelines and slow erosion heightened by the climate crisis. Reducing erosion and the resulting sediment disposition could save rural communities millions by extending the years between dredging.
The ExoForms imitate nature, providing structure for grasses and habitat to develop, unlike floodwalls.
“We are big advocates in Virginia, in particular, for building with biomimicry,” Nelson said. “We should build lighter, smarter, more biological. And the public sector, in particular, shouldn’t be doing these giant monstrosities (like riprap and walls).”
Lewie Lawrence, the executive director of the Middle Peninsula Planning District, learned about Natrx at a climate conference some years ago and realized the company had a cost-effective and aesthetically pleasing solution to slow flooding and reduce the costs of dredging, an economic lifeline helping to keep the local fishery industry healthy.
He shepherded a project on the East River to protect a private residence with custom ExoForms that used a 3-D simulation created with a drone so the homeowners could envision the result. Then he collaborated with the National Oceanic and Atmospheric Administration and the National Fish and Wildlife Administration to fund a much larger $1 million project protecting Hog Island in Gloucester, which NOAA had targeted for habitat restoration.
For Hog Island, Natrx custom designed 972 feet of interlocking ExoForms for high-wave energy areas and 122 feet for low-energy oyster reefs, providing surface area for potentially 14 million oysters. The company said the project will prevent 40,000 tons of eroding sediment from flowing into the Bay.
This video shows an ExoForm breakwater at Hog Island (Mobjack bay / York River), a project in partnership with Biogenic Solutions Consulting LLC. Hog Island and the surrounding area is a critical habitat that protects the middle Penninsula from large storms, and also protects and supports one of the largest fish nurseries and submerged aquatic vegetation beds in the United States. (Leonard Nelson/Natrx)
While those forms were manufactured with traditional concrete, Natrx is moving forward with plans to mass-produce concrete with the dredging spoils. It’s looking to build plants and is partnering with Titan America, a Norfolk company that recently was awarded a $61.7 million grant by the U.S. Department of Energy to develop a plant outside Roanoke using clay dredging spoils to manufacture the more environmentally-friendly cement.
‘It’s great when you can find the win, win, win,” said Troy Hartley, director of the Virginia Sea Grant program, which partners with RISE and has been working with Natrx.
Looking ahead
Hartley sees the market for dredging concrete limited only by imagination. It could be used to 3-D print the walls of buildings to grow plants, cooling urban heat islands. Builders could print the foundation of a raised house with the expectation it will be moved in a couple of decades as sea levels rise. When that happens, the foundation left behind would become an oyster reef.
“It’s that forward-thinking innovation about future opportunities with this technology that’s got to be the core of our innovation ecosystem,” he added.
Bringing Natrx’s green concrete to the Middle Peninsula and elsewhere, though, will require navigating the maze of manufacturing and permitting.
The company has raised $6.2 million from investors, including a seed round led by Ponderosa Ventures, a firm co-founded by former presidential candidate and hedge fund manager Tom Steyer.
“We’re well capitalized. We’re growing relatively quickly,” Nelson said. “We’ve got just shy of 50 projects in the water.”
Nelson envisions a series of plants creating concrete with spoils near where dredging takes place and shoreline resilience is needed. He pictures one on the site of the Middle Peninsula Regional Airport in West Point.
To promote that project, the company commissioned a feasibility study by Mangum Economics. Natrx, its employers, and suppliers would support 183 jobs, over $10 million in pay and benefits, and almost $107 million in economic activity in the Middle Peninsula, according to the report. Because Natrx plans to purchase supplies from Virginia companies, it would also support an additional 89 jobs, more than $10 million in pay and benefits, and more than $34 million of economic activity in Virginia, beyond the Middle Peninsula.
“Our next step is we need to resource a study to figure out how long is this going to take,” Nelson said, noting the process that will likely span years.
For Lawrence, who has been working on the airport site project, Natrx fits into the planning district’s Fight the Flood program and the goal of turning flooding threats into economic opportunity as a laboratory and landing spot for innovative companies. Turning trash into treasure by converting spoils into useful material is symbolic of that mission.
“For years, it has always been referred to as a waste product,” he said. “And now it’s not. It’s a raw material with incredible value.”
Virginia Mercury is part of States Newsroom, a nonprofit news network supported by grants and a coalition of donors as a 501c(3) public charity.